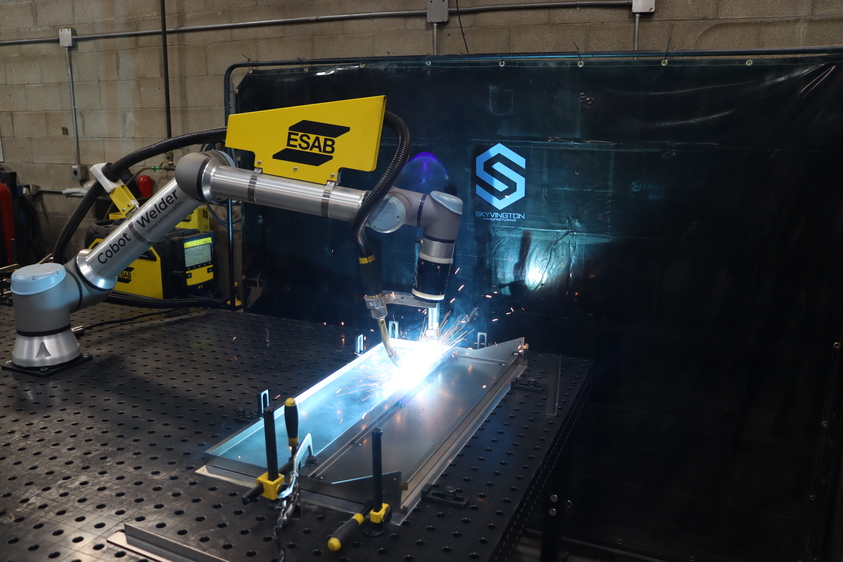
Transform Your Welding Shop with Cobot Welding: A Comprehensive Guide
- Cobots are a subset of programmable machines designed to perform tasks safely and effectively in a human environment.
- They offer improved productivity, quality, and safety while reducing operating cost and worker injuries.
- Cobots are easier to program than traditional robots and integrate seamlessly into existing workspaces without a need to modify the space for a larger robot. The smaller size makes cobots ideal for light-duty applications.
Understanding Cobot Welding and its Benefits
The growth of automation in manufacturing has been widely publicised over the past few decades, however, advancements in one specific task have captured our attention: industrial welding.
Industrial welding robots have existed for decades, so what makes the technology stand out today?
Is now a good time to purchase a robot welder?
To help you explore this type of investment, we will answer some common questions, review previous challenges, outline system components, touch on safety considerations, and discuss costs associated with owning a robot welder.
First, let us define the word ‘Cobot’, which was first introduced in 1996.
What is a Cobot?
The term ‘cobot’ is short for “collaborative robot”. Cobots are a subset of programmable machines designed to perform tasks safely and effectively in a human environment. Cobots can work next to people without modifying the shop floor or requiring a fenced-off area. Remember: “All Cobots are Robots, but not all Robots are Cobots”.
Collaborative robot welding, or ‘cobot welding’, is gaining traction because it can solve today’s toughest challenges in the most demanding environments, including industries with a high mix of low-volume parts. This allows for increased output and productivity – without more manpower– all within a small footprint. This is especially impactful for companies that are feeling the pinch of the welder shortage (which is everyone).
Traditional, non-collaborative robots are often referred to as “industrial robots”. Industrial robots are the large systems that are often used in the automotive industry, working around a car chassis without a single person nearby. Industrial robots require highly trained programmers and extensive systems investments. In today’s tight labor market, this simply means you will substitute the challenge of hiring a skilled tradesperson with the obstacle of hiring multiple skilled robot programmers.
Benefits of Cobot Welding
Robots can make your life easier, as long as you’re matched to the right type of system. For businesses where large industrial robot installations are cost-prohibitive, cobots may be the ideal solution. These businesses find that cobot welding systems are both cost-effective and easy to install.
There are numerous benefits to integrating cobot welding into your production process, including but not limited to:
- Increased productivity: Cobots can operate with a repeatable operation time, making it easier to schedule the upstream and downstream steps in the value stream.
- Improved quality: Cobots produce repeatable high-quality welds.
- Enhanced safety: The integrated safety features decrease the risk of workplace accidents.
- Reduced cost: With the ability to perform tasks accurately, cobots can significantly decrease rework and repair costs.
- Decreased injuries: With cobots shouldering repeatable tasks, the risk of repetitive strain injuries (RSI) or overuse fatigue decreases.
We receive many questions about the transition away from manual welding. Many of these questions revolve around initial investment costs, setup time, training, and the implications for their existing team members.
Frankly, all questions are the right questions to ask.
We will touch on a few of these questions in this article. If you have more questions or want to read more, our ESAB University has articles, videos, blog articles, and more that you can explore.
Cobot Welding Vs. Traditional Robotic Welding: What’s the Difference?
The traditional industrial welding robot operates inside of its own caged ‘box’ and does not interact with humans at any time. In lean manufacturing, these isolated areas are called “process monuments”.
Process monuments are difficult to move or integrate into one-piece flow value streams. The most cost-effective production is high-volume, low-mix (HMLV) manufacturing. On the other hand, cobot welders are easy to move and reprogram because they occupy a small footprint and can mount (or remount) almost anywhere. They are redeployed as the production backlog changes and different equipment needs to be utilized.
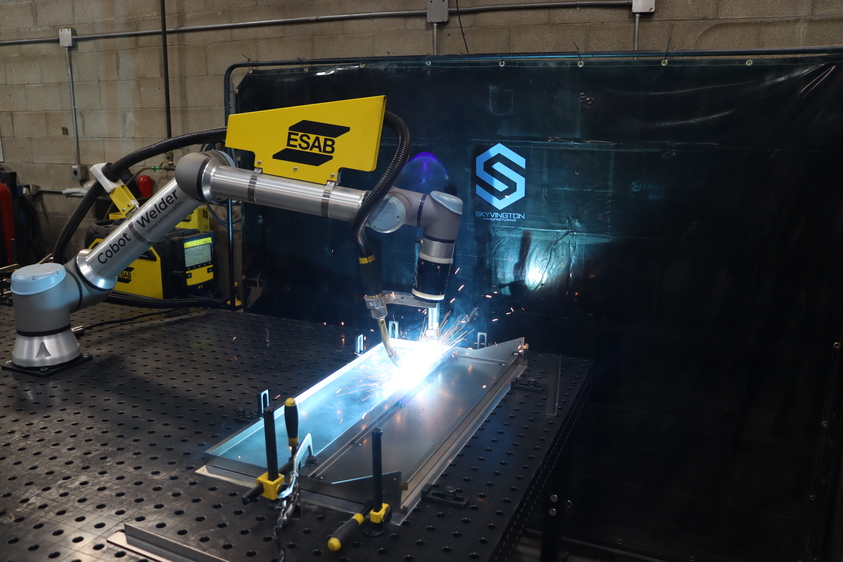
Cobot Welding | Traditional Robotic Welding | |
Ease of programming | Cobots are designed to be used by manufacturing, technical, or process experts, not someone with years of coding experience. They often support user-friendly and intuitive interfaces to assist with programming the robot. Cobots are a compact solution that can be moved to the next task. | Programming traditional robotic systems requires advanced coding skills to support the installation and upkeep of the robot. The code used depends on the robot manufacturer and requires weeks (if not months) to master. |
Payload and Speed | Cobots operate at lower speeds and payloads for light-duty applications that encourage human collaboration. | Traditional industrial robotic systems operate at higher payloads and speeds, which is ideal for heavy-duty and fast-paced operation. These factors do not promote close human proximity. |
Safety | Cobots are designed with the assumption that a person could come in contact with the robot at any time. Safety functions inherent to the cobot employ sensors to monitor the motion, speed, force, and power of the cobot relative to a person’s proximity. If risk assessments are done correctly, traditional guards or protective devices are not needed to maintain functional safety. | Traditional industrial welding robots are designed with the assumption that a person would never enter into the restricted zone at any time during operation. As a result, these robots operate at high speeds and force. Compliance with current safety standards must be maintained, including but not limited to physical barriers, safety scanners, and emergency stops. |
Cost | The initial investment of the cobot may be higher. However, installation costs are consistently lower when accounting for the lack of specialized safety infrastructure. Operating costs are lower due to their ability to perform diverse tasks. Cobots also require less training and certification to program the robot. | The initial investment cost seems low when assessing the robot alone. However, additional safety infrastructure must be accounted for in the investment. Additionally, operations must determine the process to bring materials to and from the robot cell. Dedicated programming and maintenance resources are required to maintain the whole system. |
Workspace | Cobots are designed to work in a human environment. This means the cobot is installed at the original workstation. Modifications to accommodate a large robot and its associated safety barriers are not required since the footprint of the cobot is significantly smaller. | Traditional robots are isolated with plenty of space and physical safety barriers. Depending on the size, the robot may have significant electrical and weight demands on the facility. As a result, the robot system requires significant floor space and pressure on the infrastructure. Inputs and outputs are moved in and out of the area in batches. |
It is important to note that the choice between a cobot welder and a traditional robot welder is not a matter of which is ‘better’ overall, but rather which is better suited to your specific operational needs and constraints.
The Upside to Programming A Cobot
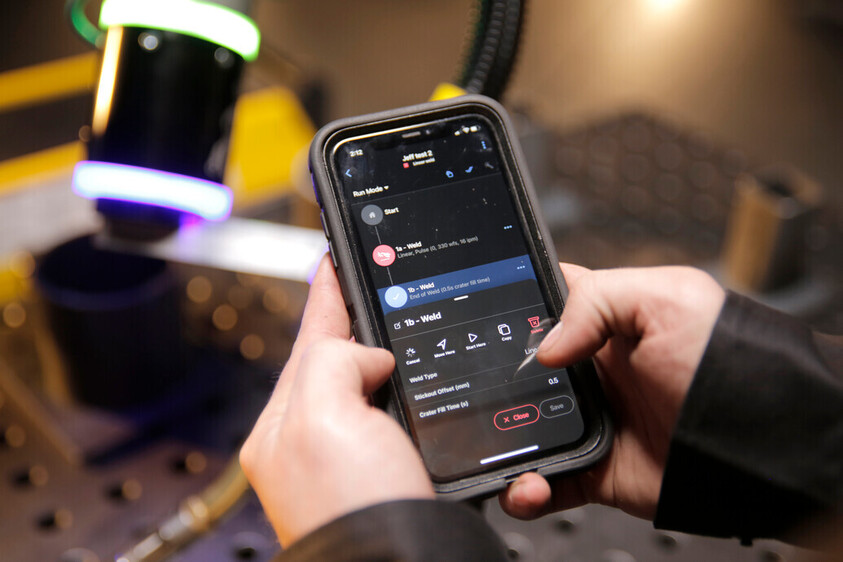
Traditional robot welding systems are often marked by complex and intricate coding requirements. They may use Python, C++, or their proprietary programming language developed from other languages. Training is focused on learning the code that is specific to the robot. These systems necessitate a high level of expertise and lengthy programming periods before they can fully function. Additionally, any changes in the process (i.e. welding on a new shape) require new code, meaning operational downtime.
The majority of robot programming is done through a hand-held “teach box” or “teach pendant”. This enables the user to communicate with the robot to program, test, and troubleshoot. Cobot welding stands out from other types of machines due to its programming simplicity. Unlike industrial robots, the programmer interacts with a visual representation of the code instead of the raw code. This means that a broader audience can program and reprogram the robot with a fraction of the downtime.
How to Program a Welding Cobot
There are many different welding cobots on the market, but in general, they follow the same workflow. Here is a simple step-by-step example of how to teach a welding cobot:
- Create a New Program: Create a new program for a part or an assembly.
- Set the welding parameters: Define the welder’s settings, such as amperage, arc length, wire speed, torch angle.
- Position the Cobot: Manually position the cobot arm to the desired starting point of the weld.
- Record Points: Use the teach pendant to record the start and end points of the weld. Record any intermediate points.
- Playback: Watch as the cobot repeats the recorded points. Adjust the speed and fine-tune the positions as required.
- Repeat: Repeat the process for each new weld path.
Note: While cobot welding systems are designed to be intuitive, training may be required to become proficient in their use. It is also important to adhere to safety protocols when working with any robots, including cobots.
Benefits of Easy Programming
Now that we have reduced (can we say eliminated?) the programming barrier, let us review a few of the measurable benefits of these cobot welders.
- Reduced Downtime: Fast and simple programming means less time spent on setting up the robot, resulting in decreased downtime and increased production.
- Improved Flexibility: The ease of programming allows for quick adjustments on the cobot, making it adaptable to changing and adding to its task list.
- Lowered Barrier to Entry: With anyone able to learn cobot programming, the barrier to entry for small to medium-sized businesses has been eliminated.
To summarize, while traditional robot welding has its strengths, the ease of programming, flexibility, and safety of cobot welding make it a compelling option for fabricators of all sizes. It is important to note that successful implementation depends on a variety of factors, such as the nature of the welding tasks, the skill level of the workforce, and the specific production demands of the business. This is where the experts of ESAB can help. If you have a specific group of tasks in mind, contact us here.
Components of a Cobot Welding System
The cobot welding system combines a collaborative robotic arm and the welding equipment. The arm, often equipped with a welding torch, follows set paths to execute welding tasks. Its precision ensures accuracy and consistency in the process. The welding equipment supplies power and materials like welding wire or shielding gas. These components form an effective and safe collaborative welding system.
A cobot welding cell comprises several integral components. These include:
- The cobot arm, its controller and its teach pendant.
- A welding power source.
- Welding equipment, including a welding torch, wire feeder, and shielding gas supply.
- PPE to protect both the cobot and human operators (similar to manual welding).
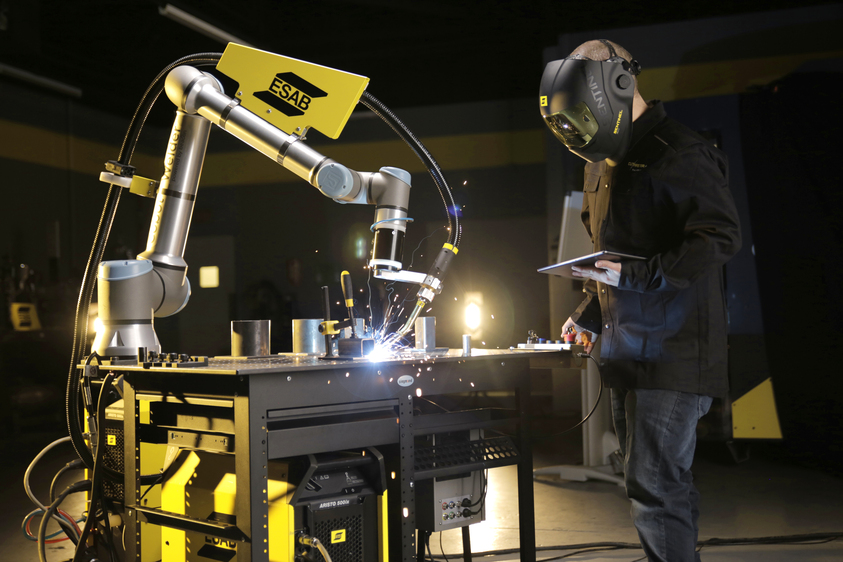
Safety Considerations When Implementing Cobot Welding
Welding Safety
Cobot welders are fun to work with, but we must take the time to highlight a few safety considerations. Robotic welding, like manual welding, presents certain potential hazards that must be mitigated to ensure the well-being of the human workforce. Appropriate safety measures should be taken to eliminate or reduce the risk of injury or damage to equipment. Despite the inherent safety design of cobots, particular attention must be paid to creating a safe and efficient welding environment. This includes but is not limited to:
- Physical Hazards: Eliminate all preventable collisions or unwanted contact with the welding equipment
- Electrical Hazards: Maintain proper safety protocols to prevent electrical shock, fire, and explosion.
- Chemical and Fume Hazards: While the cobot is unable to breathe in metallic oxides, silicates, and fluorides, it is important to ensure the humans in the area are wearing the appropriate PPE and maintain adequate ventilation in the workspace.
Risk Assessment
All robot installations must conduct a thorough risk assessment, which is a formal process to ensure the robot integration is safe to use. The risk assessments document and quantify the hazards and selected solutions. For cobots, collaborative robot safety standards ISO-10218 and TS-15066 apply. ISO-10218 describes safety requirements for industrial robots, while TS-15066 supplements this standard with guidance for industrial-only cobot systems and workplace safety.
OSHA outlines some examples and best practices for conducting an effective risk assessment (RA). For each action (task) there is an associated hazard, calculated risk level, documented safety solution, and new risk level. The output of the assessment is the required safety function and the functional risk reduction measures for each function. An excerpt from an example Risk Assessment is shown below.
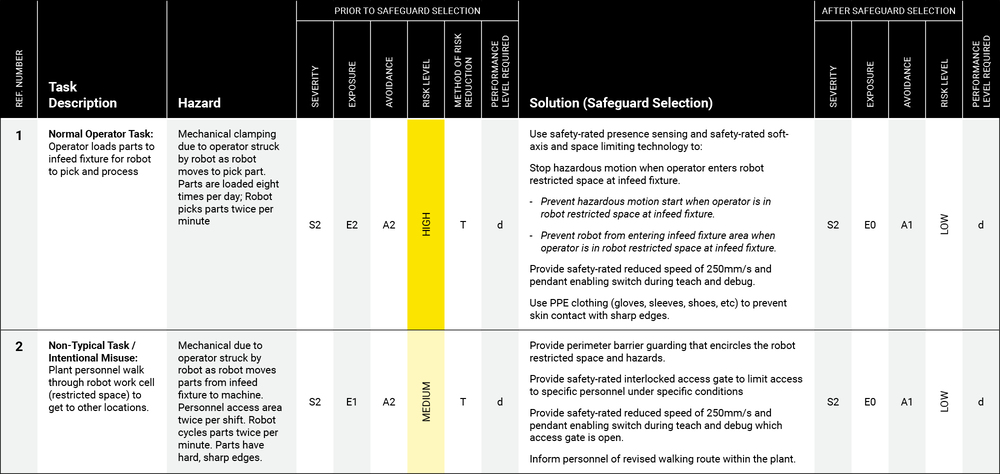
Risk assessments should be periodically reviewed and validated. A risk assessment will show the solution but will not capture the status of that action. This is why a task list (or action list) should be an output of the RA. The task list will assign a person and a due date to each task. The task list should be reviewed with scheduled frequency to ensure all actions are completed on time.
The Cost of Cobot Welding: A Breakdown
The cost of a cobot welding system can be divided into three main categories: acquisition, programming, and maintenance costs. Cobot training would be needed, but consumes only hours of a technician’s time (vs. weeks).
Acquisition Costs | The acquisition cost is the initial purchase of the cobot, welding equipment, and the necessary peripherals. This cost can vary widely depending on the robot platform. Contact the ESAB Team to inquire about the costs of a welding cobot. |
Programming Costs | Cobot welders are known for their seamless programming process. This advantage removes the need for skilled programming or attending time-consuming training, significantly reducing cost. |
Maintenance Costs | Cobot systems tend to have lower maintenance costs than traditional robotic systems due to their simpler design and construction. The robot maintenance includes costs related to the upkeep of safety measures, which are generally lower for cobot systems due to their inherent focus on operator safety. |
Potential Returns on Investment
For shop owners, the decision to invest in a cobot welder should not solely be driven by the initial cost/benefit calculation, but rather by the ongoing return on investment. The labor crunch we are experiencing today is expected to get worse.
The American Welding Society estimates that by 2024 there will be a shortage of 400,000 welders here in the US. Canada expects openings and job seeker number to remain similar, projecting the current welder shortage to extend through the next five years at least. To make things worse, the average age of a welder in the US is 55. It is no surprise that small and medium enterprises (SMEs) are also looking to invest in cobot welding solutions.
Here are a few ROI’s that our customers have highlighted:
- Increased Productivity: Cobot welding systems are well known for their efficiency. They can operate 24/7, effectively bypassing human limitations such as fatigue. This can significantly increase the fabricator’s output, leading to higher revenues and profitability.
- Reduced Errors and Rework: Unlike humans, Cobots are not prone to making errors due to distraction, fatigue, or inexperience. This leads to a repeatable high-quality output and reduces the costs related to rework and waste.
- Lower Labor Costs: Cobots do not eliminate people, they assist them. Cobots allow the operator to focus on more complex tasks, thereby increasing production. This means a higher hourly production rate with the same (or lower) labor cost.
- Enhanced Safety: Cobot welding systems are designed with operator safety in mind, reducing the risk of workplace accidents. Worker fatigue increases the risk of accidents, but consistent cobot operation enables a consistent, safe environment. This can result in lower insurance premiums and compensation payouts.
While the initial investment of a cobot is like any other machine purchase, the long-term financial benefits of adopting cobot welding systems can be substantial. Investing in Cobot welding systems can be a strategic move for fabricators, facilitating enhanced productivity, higher quality output, cost savings, and improved safety. It is the long-term benefits that should be the focus when considering the return on investment.
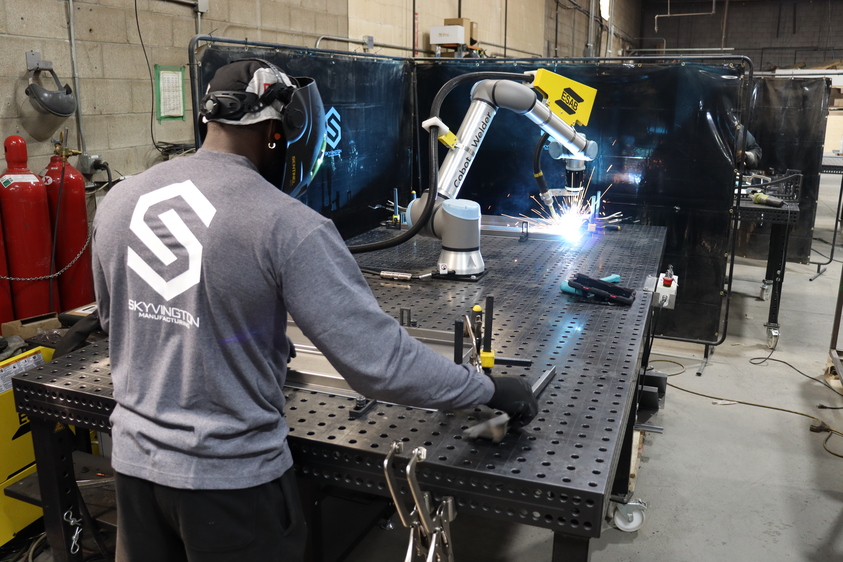
More small businesses, such as Skyvington Manufacturing Inc., are adopting cobot welders as their backlog grows. Skyvington Manufacturing Inc. is a 30-person shop in Mississauga, Ontario, Canada that turned to a cobot welding solution when its backlog kept getting longer. President Brett Skyvington explains their rationale:
“One of the reasons I looked for the cobot was that our welding department was booked out for five weeks solid, and customer lead times were getting pushed out.”
After a month of using a cobot welder, the cobot made over 25,000 welds and tackled a large order for the company.
“The cobot allows us to achieve our quality standards and produce in a timely fashion, at a cost-effective rate. That’s really what we strive for as a company,” says Skyvington.
Conclusion
There is a lot to consider as you investigate a cobot welder. All of your questions are the right questions. We recognize that you may be considering changes due to difficulty hiring experienced welders, the pressures of a growing backlog, or the desire to expand into additional industrial segments.
In this article, we answered some common questions, reviewed challenges, outlined system components, touched on safety considerations, and discussed costs associated with owning a robot welder.
The easiest way to know whether cobot welding could help is to reach out for a virtual demo. At ESAB, we have been in business for over 100 years and have solved many of these challenges for our client partners. We can support you in your next steps. When you are ready to discuss your project, contact us here.
Cobot Welding FAQ
How fast can a cobot welding system weld?
The complexity of the task can vary widely. On average, a cobot welder can weld at a speed of about 20 to 30 inches per minute. However, it’s not only about speed. Some of the benefits of a cobot welding system are the precision, consistency, and ability to operate around the clock.
Can I teach a welding cobot even though I do not have experience in programming or robotics?
Yes! Programming a welding cobot is different from coding a robot. You do not need to have any coding experience when teaching a cobot. Cobots have intuitive user interfaces (including phone apps) that simplify the programming process.
Request a virtual demo to see how this works.
How can I get started with a cobot welder?
First, contact us or request a demo. We will collaborate with you to determine the right size system for you. We will also get you started by sharing installation, startup, and training procedures developed by our team.
I operate a small shop. Can I still use a cobot welder?
Yes! Cobot welders are ideal for small-scale welding operations. Their compact size and flexible programming capabilities make them perfect for welding tasks in smaller workspaces. You can easily integrate the cobot into existing welding setups, allowing small-scale fabricators like you to automate their welding processes without significant infrastructure changes.